પ્લાયવુડ લાકડાના ત્રણ કે તેથી વધુ પાતળા સ્તરોથી બનેલું હોય છે જે એડહેસિવ સાથે જોડાયેલા હોય છે. લાકડાના દરેક સ્તર, અથવા પ્લાય, સામાન્ય રીતે સંકોચન ઘટાડવા અને ફિનિશ્ડ ટુકડાની મજબૂતાઈ સુધારવા માટે, તેના દાણાને બાજુના સ્તર સાથે કાટખૂણે રાખીને દિશામાન કરવામાં આવે છે. મોટાભાગના પ્લાયવુડને મકાન બાંધકામમાં ઉપયોગમાં લેવાતી મોટી, સપાટ શીટ્સમાં દબાવવામાં આવે છે. ફર્નિચર, બોટ અને વિમાનમાં ઉપયોગ માટે અન્ય પ્લાયવુડ ટુકડાઓ સરળ અથવા સંયોજન વળાંકોમાં બનાવી શકાય છે.
બાંધકામના સાધન તરીકે લાકડાના પાતળા સ્તરોનો ઉપયોગ આશરે 1500 બીસીમાં થયો હતો જ્યારે ઇજિપ્તીયન કારીગરોએ રાજા તુત-અંખ-અમોનની કબરમાં મળેલા દેવદાર કાસ્કેટના બાહ્ય ભાગ સાથે ઘેરા આબનૂસ લાકડાના પાતળા ટુકડાઓ બાંધ્યા હતા. આ તકનીકનો ઉપયોગ પાછળથી ગ્રીક અને રોમન લોકો દ્વારા સુંદર ફર્નિચર અને અન્ય સુશોભન વસ્તુઓ બનાવવા માટે કરવામાં આવ્યો હતો. 1600 ના દાયકામાં, લાકડાના પાતળા ટુકડાઓથી ફર્નિચરને સજાવવાની કળાને વેનીયરિંગ તરીકે ઓળખવામાં આવી, અને તે ટુકડાઓ પોતે વેનીયર તરીકે જાણીતા બન્યા.
૧૭૦૦ ના દાયકાના અંત સુધી, વેનીયરના ટુકડા સંપૂર્ણપણે હાથથી કાપવામાં આવતા હતા. ૧૭૯૭ માં, અંગ્રેજ સર સેમ્યુઅલ બેન્થમે વેનીયર બનાવવા માટે અનેક મશીનોને આવરી લેતા પેટન્ટ માટે અરજી કરી. તેમની પેટન્ટ અરજીઓમાં, તેમણે વેનીયરના અનેક સ્તરોને ગુંદર સાથે લેમિનેટેડ કરીને જાડા ટુકડા બનાવવાની વિભાવનાનું વર્ણન કર્યું - જેને આપણે હવે પ્લાયવુડ કહીએ છીએ તેનું આ પહેલું વર્ણન છે.
આ વિકાસ છતાં, ફર્નિચર ઉદ્યોગની બહાર લેમિનેટેડ વેનીયરનો કોઈ વ્યાપારી ઉપયોગ થતો જોવા મળે તે પહેલાં લગભગ સો વર્ષ લાગ્યા. લગભગ 1890 માં, દરવાજા બનાવવા માટે લેમિનેટેડ લાકડાનો ઉપયોગ સૌપ્રથમ કરવામાં આવ્યો. માંગ વધતાં, ઘણી કંપનીઓએ મલ્ટીપલ-પ્લાય લેમિનેટેડ લાકડાની શીટ્સનું ઉત્પાદન શરૂ કર્યું, જે ફક્ત દરવાજા માટે જ નહીં, પરંતુ રેલરોડ કાર, બસો અને વિમાનોમાં પણ ઉપયોગ માટે હતી. આ વધતા ઉપયોગ છતાં, "પેસ્ટેડ લાકડા" નો ઉપયોગ કરવાની વિભાવના, જેમ કે કેટલાક કારીગરો તેમને કટાક્ષમાં કહે છે, તેણે ઉત્પાદન માટે નકારાત્મક છબી બનાવી. આ છબીનો સામનો કરવા માટે, લેમિનેટેડ લાકડા ઉત્પાદકો મળ્યા અને અંતે નવી સામગ્રીનું વર્ણન કરવા માટે "પ્લાયવુડ" શબ્દ પર સમાધાન કર્યું.
૧૯૨૮માં, યુનાઇટેડ સ્ટેટ્સમાં સામાન્ય બાંધકામ સામગ્રી તરીકે ઉપયોગ માટે પ્રથમ પ્રમાણભૂત કદના ૪ ફૂટ બાય ૮ ફૂટ (૧.૨ મીટર બાય ૨.૪ મીટર) પ્લાયવુડ શીટ્સ રજૂ કરવામાં આવી હતી. પછીના દાયકાઓમાં, સુધારેલા એડહેસિવ્સ અને ઉત્પાદનની નવી પદ્ધતિઓએ પ્લાયવુડનો ઉપયોગ વિવિધ પ્રકારના ઉપયોગ માટે કરવાની મંજૂરી આપી. આજે, પ્લાયવુડે ઘણા બાંધકામ હેતુઓ માટે કાપેલા લાકડાનું સ્થાન લીધું છે, અને પ્લાયવુડ ઉત્પાદન એક અબજો ડોલરનો વિશ્વવ્યાપી ઉદ્યોગ બની ગયો છે.
પ્લાયવુડના બાહ્ય સ્તરોને અનુક્રમે ફેસ અને બેક તરીકે ઓળખવામાં આવે છે. ફેસ એ સપાટી છે જેનો ઉપયોગ અથવા દૃશ્યમાન ઉપયોગ થાય છે, જ્યારે પાછળનો ભાગ બિનઉપયોગી અથવા છુપાયેલ રહે છે. મધ્ય સ્તરને કોર તરીકે ઓળખવામાં આવે છે. પાંચ કે તેથી વધુ પ્લાયવુડમાં, ઇન્ટર-મધ્યસ્થી સ્તરોને ક્રોસબેન્ડ તરીકે ઓળખવામાં આવે છે.
પ્લાયવુડ હાર્ડવુડ્સ, સોફ્ટવુડ્સ અથવા બંનેના મિશ્રણમાંથી બનાવી શકાય છે. કેટલાક સામાન્ય હાર્ડવુડ્સમાં રાખ, મેપલ, મહોગની, ઓક અને સાગનો સમાવેશ થાય છે. યુનાઇટેડ સ્ટેટ્સમાં પ્લાયવુડ બનાવવા માટે વપરાતું સૌથી સામાન્ય સોફ્ટવુડ ડગ્લાસ ફિર છે, જોકે પાઈન, દેવદાર, સ્પ્રુસ અને રેડવુડની ઘણી જાતોનો પણ ઉપયોગ થાય છે.
કમ્પોઝિટ પ્લાયવુડમાં પાર્ટિકલબોર્ડ અથવા ઘન લાકડાના ટુકડાઓનો બનેલો કોર હોય છે જે ધારથી ધાર સુધી જોડાયેલ હોય છે. તે પ્લાયવુડ વેનીયરના આગળના ભાગ અને પાછળના ભાગથી પૂર્ણ થાય છે. જ્યાં ખૂબ જાડા શીટ્સની જરૂર હોય ત્યાં કમ્પોઝિટ પ્લાયવુડનો ઉપયોગ થાય છે.
લાકડાના સ્તરોને એકસાથે જોડવા માટે વપરાતા એડહેસિવનો પ્રકાર ફિનિશ્ડ પ્લાયવુડના ચોક્કસ ઉપયોગ પર આધાર રાખે છે. માળખાના બાહ્ય ભાગ પર ઇન્સ્ટોલેશન માટે રચાયેલ સોફ્ટવુડ પ્લાયવુડ શીટ્સ સામાન્ય રીતે એડહેસિવ તરીકે ફિનોલ-ફોર્માલ્ડિહાઇડ રેઝિનનો ઉપયોગ કરે છે કારણ કે તેની ઉત્તમ શક્તિ અને ભેજ સામે પ્રતિકાર હોય છે. માળખાના આંતરિક ભાગ પર ઇન્સ્ટોલેશન માટે રચાયેલ સોફ્ટવુડ પ્લાયવુડ શીટ્સ બ્લડ પ્રોટીન અથવા સોયાબીન પ્રોટીન એડહેસિવનો ઉપયોગ કરી શકે છે, જોકે મોટાભાગની સોફ્ટવુડ આંતરિક શીટ્સ હવે બાહ્ય શીટ્સ માટે વપરાતા સમાન ફિનોલ-ફોર્માલ્ડિહાઇડ રેઝિનથી બનાવવામાં આવે છે. આંતરિક ઉપયોગો માટે અને ફર્નિચરના નિર્માણમાં ઉપયોગમાં લેવાતા હાર્ડવુડ પ્લાયવુડ સામાન્ય રીતે યુરિયા-ફોર્માલ્ડિહાઇડ રેઝિનથી બનાવવામાં આવે છે.
કેટલાક ઉપયોગો માટે પ્લાયવુડ શીટ્સની જરૂર પડે છે જેમાં પ્લાસ્ટિક, ધાતુ અથવા રેઝિનથી ભરેલા કાગળ અથવા ફેબ્રિકનો પાતળો પડ હોય છે જે આગળ અથવા પાછળ (અથવા બંને) સાથે જોડાયેલ હોય છે જેથી બાહ્ય સપાટીને ભેજ અને ઘર્ષણ સામે વધારાનો પ્રતિકાર મળે અથવા તેના પેઇન્ટ-હોલ્ડિંગ ગુણધર્મોમાં સુધારો થાય. આવા પ્લાયવુડને ઓવરલેડ પ્લાયવુડ કહેવામાં આવે છે અને તેનો ઉપયોગ સામાન્ય રીતે બાંધકામ, પરિવહન અને કૃષિ ઉદ્યોગોમાં થાય છે.
સપાટીઓને પૂર્ણ દેખાવ આપવા માટે અન્ય પ્લાયવુડ શીટ્સને પ્રવાહી ડાઘથી કોટેડ કરી શકાય છે, અથવા પ્લાયવુડની જ્યોત પ્રતિકાર અથવા સડો સામે પ્રતિકાર સુધારવા માટે વિવિધ રસાયણોથી સારવાર કરી શકાય છે.
પ્લાયવુડના બે વ્યાપક વર્ગો છે, દરેકની પોતાની ગ્રેડિંગ સિસ્ટમ છે.
એક વર્ગને બાંધકામ અને ઔદ્યોગિક તરીકે ઓળખવામાં આવે છે. આ વર્ગના પ્લાયવુડનો ઉપયોગ મુખ્યત્વે તેમની મજબૂતાઈ માટે થાય છે અને તેમની એક્સપોઝર ક્ષમતા અને આગળ અને પાછળ ઉપયોગમાં લેવાતા વેનીયરના ગ્રેડ દ્વારા રેટ કરવામાં આવે છે. એક્સપોઝર ક્ષમતા ગુંદરના પ્રકાર પર આધાર રાખીને આંતરિક અથવા બાહ્ય હોઈ શકે છે. વેનીયર ગ્રેડ N, A, B, C, અથવા D હોઈ શકે છે. N ગ્રેડમાં સપાટી પર ખૂબ ઓછી ખામીઓ હોય છે, જ્યારે D ગ્રેડમાં અસંખ્ય ગાંઠો અને સ્પ્લિટ હોઈ શકે છે. ઉદાહરણ તરીકે, ઘરમાં સબફ્લોરિંગ માટે વપરાતા પ્લાયવુડને "ઇન્ટિરિયર CD" રેટિંગ આપવામાં આવે છે. આનો અર્થ એ છે કે તેનો પાછળ D બેક સાથે C ફેસ છે, અને ગુંદર સુરક્ષિત સ્થળોએ ઉપયોગ માટે યોગ્ય છે. બધા બાંધકામ અને ઔદ્યોગિક પ્લાયવુડના આંતરિક પ્લાય ગ્રેડ C અથવા D વેનીયરમાંથી બનાવવામાં આવે છે, પછી ભલે તે રેટિંગ ગમે તે હોય.
પ્લાયવુડનો બીજો વર્ગ હાર્ડવુડ અને સુશોભન તરીકે ઓળખાય છે. આ વર્ગના પ્લાયવુડનો ઉપયોગ મુખ્યત્વે તેમના દેખાવ માટે થાય છે અને ભેજ પ્રતિકારના ઉતરતા ક્રમમાં વર્ગીકૃત કરવામાં આવે છે જેમ કે ટેકનિકલ (બાહ્ય), પ્રકાર I (બાહ્ય), પ્રકાર II (આંતરિક), અને પ્રકાર III (આંતરિક). તેમના ફેસ વેનિયર્સ લગભગ ખામીઓથી મુક્ત છે.
કદ
પ્લાયવુડ શીટ્સની જાડાઈ 06 ઇંચ (1.6 મીમી) થી 3.0 ઇંચ (76 મીમી) સુધીની હોય છે. સૌથી સામાન્ય જાડાઈ 0.25 ઇંચ (6.4 મીમી) થી 0.75 ઇંચ (19.0 મીમી) ની રેન્જમાં હોય છે. જોકે પ્લાયવુડ શીટનો મુખ્ય ભાગ, ક્રોસબેન્ડ અને ચહેરો અને પાછળનો ભાગ વિવિધ જાડાઈના વેનીયરથી બનેલો હોઈ શકે છે, દરેકની જાડાઈ કેન્દ્રની આસપાસ સંતુલિત હોવી જોઈએ. ઉદાહરણ તરીકે, ચહેરો અને પાછળનો ભાગ સમાન જાડાઈના હોવા જોઈએ. તેવી જ રીતે ઉપર અને નીચેના ક્રોસબેન્ડ સમાન હોવા જોઈએ.
ઇમારતોના બાંધકામમાં વપરાતા પ્લાયવુડ શીટ્સ માટે સૌથી સામાન્ય કદ 4 ફૂટ (1.2 મીટર) પહોળાઈ અને 8 ફૂટ (2.4 મીટર) લાંબી છે. અન્ય સામાન્ય પહોળાઈ 3 ફૂટ (0.9 મીટર) અને 5 ફૂટ (1.5 મીટર) છે. લંબાઈ 1 ફૂટ (0.3 મીટર) વધારામાં 8 ફૂટ (2.4 મીટર) થી 12 ફૂટ (3.6 મીટર) સુધી બદલાય છે. બોટ બનાવવા જેવા ખાસ કાર્યક્રમો માટે મોટી શીટ્સની જરૂર પડી શકે છે.
પ્લાયવુડ બનાવવા માટે વપરાતા વૃક્ષો સામાન્ય રીતે લાકડા બનાવવા માટે વપરાતા વૃક્ષો કરતા નાના વ્યાસના હોય છે. મોટાભાગના કિસ્સાઓમાં, તેઓ પ્લાયવુડ કંપનીની માલિકીના વિસ્તારોમાં વાવવામાં અને ઉગાડવામાં આવ્યા છે. આ વિસ્તારોનું કાળજીપૂર્વક સંચાલન કરવામાં આવે છે જેથી વૃક્ષોનો વિકાસ મહત્તમ થાય અને જંતુઓ અથવા આગથી થતા નુકસાનને ઓછું કરી શકાય.
વૃક્ષોને 4 ફૂટ બાય 8 ફૂટ (1.2 મીટર બાય 2.4 મીટર) પ્લાયવુડ શીટ્સમાં પ્રોસેસ કરવા માટેની કામગીરીનો એક લાક્ષણિક ક્રમ અહીં છે:
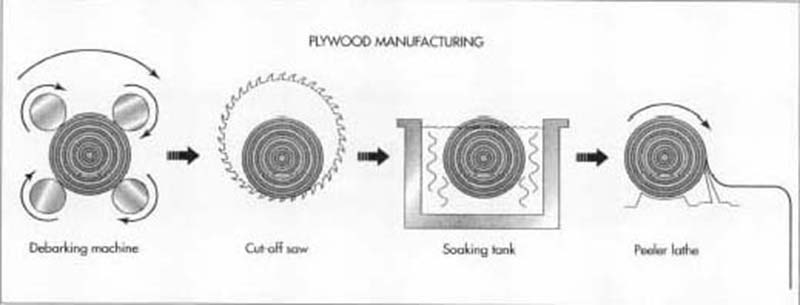
લાકડાના લાકડાને પહેલા છાલમાંથી બહાર કાઢવામાં આવે છે અને પછી તેને પીલર બ્લોક્સમાં કાપવામાં આવે છે. બ્લોક્સને વેનીયરના પટ્ટાઓમાં કાપવા માટે, તેને પહેલા પલાળીને પછી તેને છોલીને પટ્ટાઓમાં ફેરવવામાં આવે છે.
૧ કોઈ વિસ્તારમાં પસંદ કરેલા વૃક્ષોને કાપવા અથવા કાપવા માટે તૈયાર તરીકે ચિહ્નિત કરવામાં આવે છે. કાપણી ગેસોલિનથી ચાલતી ચેઈન આરી અથવા ફેલર્સ નામના પૈડાવાળા વાહનોના આગળના ભાગમાં લગાવેલા મોટા હાઇડ્રોલિક કાતરનો ઉપયોગ કરીને કરી શકાય છે. ચેઈન આરી વડે પડી ગયેલા વૃક્ષોમાંથી ડાળીઓ દૂર કરવામાં આવે છે.
2 કાપેલા ઝાડના થડ, અથવા લાકડા, સ્કિડર્સ નામના પૈડાવાળા વાહનો દ્વારા લોડિંગ એરિયામાં ખેંચાય છે. લાકડાને લંબાઈમાં કાપવામાં આવે છે અને પ્લાયવુડ મિલ સુધી જવા માટે ટ્રક પર લોડ કરવામાં આવે છે, જ્યાં તેમને લાંબા ઢગલામાં સ્ટૅક કરવામાં આવે છે જેને લોગ ડેક તરીકે ઓળખવામાં આવે છે.
૩ જેમ જેમ લોગની જરૂર પડે છે, તેમ તેમ તેમને રબરથી થાકેલા લોડરો દ્વારા લોગ ડેકમાંથી ઉપાડવામાં આવે છે અને ચેઇન કન્વેયર પર મૂકવામાં આવે છે જે તેમને ડીબાર્કિંગ મશીન સુધી લઈ જાય છે. આ મશીન છાલને દૂર કરે છે, કાં તો તીક્ષ્ણ દાંતાવાળા ગ્રાઇન્ડીંગ વ્હીલ્સ અથવા ઉચ્ચ-દબાણવાળા પાણીના જેટ સાથે, જ્યારે લોગને ધીમે ધીમે તેની લાંબી ધરી પર ફેરવવામાં આવે છે.
૪ બાર્ક કરેલા લાકડાને ચેઇન કન્વેયર પર મિલમાં લઈ જવામાં આવે છે જ્યાં એક વિશાળ ગોળાકાર કરવત તેમને લગભગ ૮ ફૂટ-૪ ઇંચ (૨.૫ મીટર) થી ૮ ફૂટ-૬ ઇંચ (૨.૬ મીટર) લાંબા ભાગોમાં કાપે છે, જે પ્રમાણભૂત ૮ ફૂટ (૨.૪ મીટર) લાંબી શીટ બનાવવા માટે યોગ્ય છે. આ લોગ વિભાગોને પીલર બ્લોક્સ તરીકે ઓળખવામાં આવે છે.
૫ વેનીયર કાપતા પહેલા, લાકડાને નરમ બનાવવા માટે પીલર બ્લોક્સને ગરમ કરીને પલાળવા જોઈએ. બ્લોક્સને બાફવામાં અથવા ગરમ પાણીમાં બોળી શકાય છે. લાકડાના પ્રકાર, બ્લોકના વ્યાસ અને અન્ય પરિબળોના આધારે આ પ્રક્રિયામાં ૧૨-૪૦ કલાક લાગે છે.
6 ગરમ કરેલા પીલર બ્લોક્સને પછી પીલર લેથમાં લઈ જવામાં આવે છે, જ્યાં તે આપમેળે ગોઠવાઈ જાય છે અને એક પછી એક લેથમાં નાખવામાં આવે છે. જેમ જેમ લેથ બ્લોકને તેની લાંબી ધરી પર ઝડપથી ફેરવે છે, તેમ તેમ પૂર્ણ-લંબાઈની છરી બ્લેડ સ્પિનિંગ બ્લોકની સપાટી પરથી 300-800 ફૂટ/મિનિટ (90-240 મીટર/મિનિટ) ની ઝડપે સતત વેનીયર શીટને છોલે છે. જ્યારે બ્લોકનો વ્યાસ લગભગ 3-4 ઇંચ (230-305 મીમી) સુધી ઘટાડી દેવામાં આવે છે, ત્યારે લાકડાનો બાકીનો ટુકડો, જેને પીલર કોર તરીકે ઓળખવામાં આવે છે, તેને લેથમાંથી બહાર કાઢવામાં આવે છે અને એક નવો પીલર બ્લોક તેની જગ્યાએ નાખવામાં આવે છે.
૭ પીલર લેથમાંથી નીકળતી લાંબી વેનીયર શીટને તાત્કાલિક પ્રક્રિયા કરી શકાય છે, અથવા તેને લાંબા, બહુ-સ્તરીય ટ્રેમાં સંગ્રહિત કરી શકાય છે અથવા રોલ પર ઘા કરી શકાય છે. કોઈ પણ સંજોગોમાં, આગળની પ્રક્રિયામાં વેનીયરને ઉપયોગમાં લઈ શકાય તેવી પહોળાઈમાં કાપવાનો સમાવેશ થાય છે, સામાન્ય રીતે લગભગ ૪ ફૂટ-૬ ઇંચ (૧.૪ મીટર), પ્રમાણભૂત ૪ ફૂટ (૧.૨ મીટર) પહોળી પ્લાયવુડ શીટ્સ બનાવવા માટે. તે જ સમયે, ઓપ્ટિકલ સ્કેનર્સ અસ્વીકાર્ય ખામીઓવાળા વિભાગો શોધે છે, અને તેમને ક્લિપ કરવામાં આવે છે, જેનાથી વેનીયરના પ્રમાણભૂત પહોળાઈ કરતા ઓછા ટુકડાઓ બાકી રહે છે.
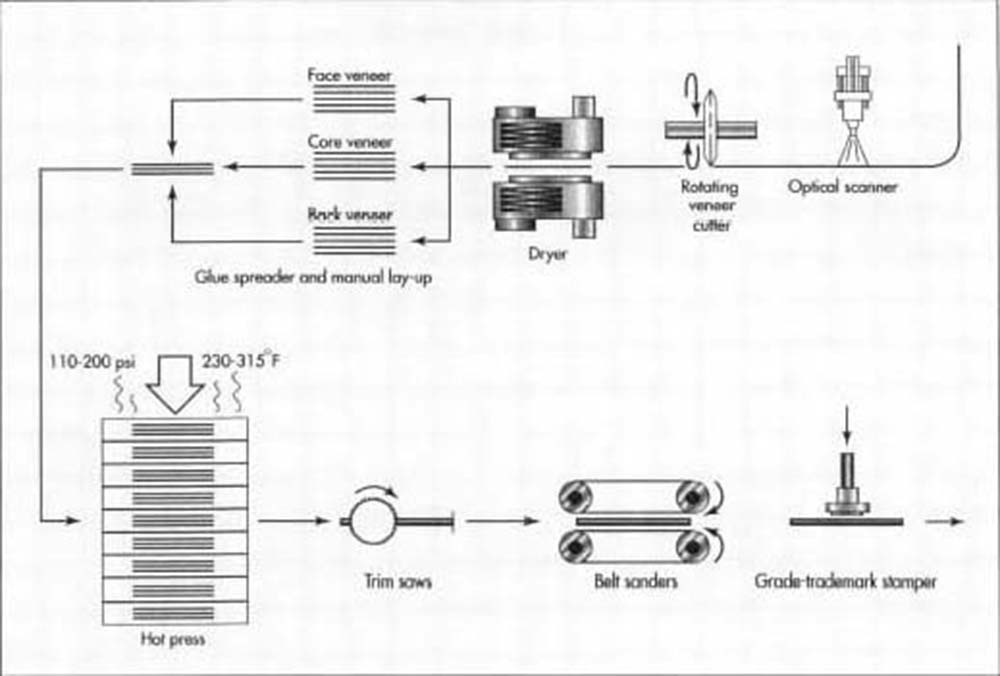
વેનીયરના ભીના પટ્ટાઓને રોલમાં ઘસવામાં આવે છે, જ્યારે ઓપ્ટિકલ સ્કેનર લાકડામાં કોઈપણ અસ્વીકાર્ય ખામીઓ શોધી કાઢે છે. સુકાઈ ગયા પછી વેનીયરને ગ્રેડ કરવામાં આવે છે અને સ્ટેક કરવામાં આવે છે. વેનીયરના પસંદ કરેલા ભાગોને એકસાથે ગુંદર કરવામાં આવે છે. પ્લાયવુડના એક નક્કર ટુકડામાં વેનીયરને સીલ કરવા માટે ગરમ પ્રેસનો ઉપયોગ કરવામાં આવે છે, જેને તેના યોગ્ય ગ્રેડ સાથે સ્ટેમ્પ કરવામાં આવે તે પહેલાં તેને ટ્રિમ અને સેન્ડ કરવામાં આવશે.
8 ત્યારબાદ વેનીયરના ભાગોને ગ્રેડ અનુસાર સૉર્ટ અને સ્ટેક કરવામાં આવે છે. આ મેન્યુઅલી કરી શકાય છે, અથવા તે ઓપ્ટિકલ સ્કેનર્સનો ઉપયોગ કરીને આપમેળે કરી શકાય છે.
9 સૉર્ટ કરેલા ભાગોને ડ્રાયરમાં નાખવામાં આવે છે જેથી તેમની ભેજ ઓછી થાય અને તેઓ એકબીજા સાથે ગુંદર ધરાવતા પહેલા સંકોચાઈ જાય. મોટાભાગની પ્લાયવુડ મિલો યાંત્રિક ડ્રાયરનો ઉપયોગ કરે છે જેમાં ટુકડાઓ ગરમ ચેમ્બરમાંથી સતત ફરે છે. કેટલાક ડ્રાયરમાં, સૂકવણી પ્રક્રિયાને ઝડપી બનાવવા માટે ટુકડાઓની સપાટી પર ઉચ્ચ-વેગ, ગરમ હવાના જેટ ફૂંકવામાં આવે છે.
૧૦ જેમ જેમ વેનીયરના ભાગો ડ્રાયરમાંથી બહાર આવે છે, તેમ તેમ તેમને ગ્રેડ મુજબ સ્ટેક કરવામાં આવે છે. પહોળાઈના ભાગોમાં ટેપ અથવા ગુંદર વડે વધારાના વેનીયર લગાવવામાં આવે છે જેથી આંતરિક સ્તરોમાં ઉપયોગ માટે યોગ્ય ટુકડાઓ બનાવવામાં આવે જ્યાં દેખાવ અને મજબૂતાઈ ઓછી મહત્વપૂર્ણ હોય છે.
૧૧ વિનીયરના તે ભાગો જે ક્રોસવેમાં સ્થાપિત કરવામાં આવશે - ત્રણ-પ્લાય શીટમાં કોર, અથવા પાંચ-પ્લાય શીટમાં ક્રોસબેન્ડ - લગભગ 4 ફૂટ-3 ઇંચ (1.3 મીટર) ની લંબાઈમાં કાપવામાં આવે છે.
૧૨ જ્યારે પ્લાયવુડના ચોક્કસ ભાગ માટે યોગ્ય વેનીયરના ભાગો ભેગા કરવામાં આવે છે, ત્યારે ટુકડાઓને એકસાથે મૂકવા અને ગુંદર કરવાની પ્રક્રિયા શરૂ થાય છે. આ મશીનો દ્વારા મેન્યુઅલી અથવા અર્ધ-સ્વચાલિત રીતે કરી શકાય છે. ત્રણ-પ્લાય શીટ્સના સૌથી સરળ કિસ્સામાં, પાછળનો વેનીયર સપાટ મૂકવામાં આવે છે અને ગ્લુ સ્પ્રેડર દ્વારા ચલાવવામાં આવે છે, જે ઉપરની સપાટી પર ગુંદરનો સ્તર લાગુ કરે છે. કોર વેનીયરના ટૂંકા ભાગો પછી ગુંદરવાળા બેકની ટોચ પર ક્રોસવે નાખવામાં આવે છે, અને આખી શીટ બીજી વખત ગ્લુ સ્પ્રેડર દ્વારા ચલાવવામાં આવે છે. અંતે, ફેસ વેનીયર ગુંદરવાળા કોરની ટોચ પર નાખવામાં આવે છે, અને શીટને પ્રેસમાં જવા માટે રાહ જોઈ રહેલી અન્ય શીટ્સ સાથે સ્ટેક કરવામાં આવે છે.
૧૩ ગુંદરવાળી શીટ્સને બહુવિધ-ખુલતા હોટ પ્રેસમાં લોડ કરવામાં આવે છે. પ્રેસ એક સમયે 20-40 શીટ્સને હેન્ડલ કરી શકે છે, દરેક શીટને અલગ સ્લોટમાં લોડ કરવામાં આવે છે. જ્યારે બધી શીટ્સ લોડ થાય છે, ત્યારે પ્રેસ તેમને લગભગ 110-200 psi (7.6-13.8 બાર) ના દબાણ હેઠળ એકસાથે દબાવી દે છે, જ્યારે તે જ સમયે તેમને લગભગ 230-315° F (109.9-157.2° C) ના તાપમાને ગરમ કરે છે. દબાણ વેનીયરના સ્તરો વચ્ચે સારો સંપર્ક સુનિશ્ચિત કરે છે, અને ગરમીને કારણે ગુંદર મહત્તમ મજબૂતાઈ માટે યોગ્ય રીતે મજબૂત થાય છે. 2-7 મિનિટના સમયગાળા પછી, પ્રેસ ખોલવામાં આવે છે અને શીટ્સ અનલોડ કરવામાં આવે છે.
૧૪ પછી ખરબચડી ચાદર કરવતના સમૂહમાંથી પસાર થાય છે, જે તેમને તેમની અંતિમ પહોળાઈ અને લંબાઈ સુધી કાપે છે. ઉચ્ચ ગ્રેડની ચાદર 4 ફૂટ (1.2 મીટર) પહોળા બેલ્ટ સેન્ડરના સમૂહમાંથી પસાર થાય છે, જે આગળ અને પાછળ બંને બાજુ રેતી કરે છે. મધ્યવર્તી ગ્રેડની ચાદરોને ખરબચડી વિસ્તારોને સાફ કરવા માટે મેન્યુઅલી સ્પોટ સેન્ડ કરવામાં આવે છે. કેટલીક ચાદરોને ગોળાકાર કરવતના બ્લેડના સમૂહમાંથી ચલાવવામાં આવે છે, જે પ્લાયવુડને ટેક્ષ્ચર દેખાવ આપવા માટે ચહેરામાં છીછરા ખાંચો કાપી નાખે છે. અંતિમ નિરીક્ષણ પછી, બાકી રહેલી કોઈપણ ખામીઓનું સમારકામ કરવામાં આવે છે.
૧૫ ફિનિશ્ડ શીટ્સ પર ગ્રેડ-ટ્રેડમાર્કનો સ્ટેમ્પ લગાવવામાં આવે છે જે ખરીદનારને એક્સપોઝર રેટિંગ, ગ્રેડ, મિલ નંબર અને અન્ય પરિબળો વિશે માહિતી આપે છે. સમાન ગ્રેડ-ટ્રેડમાર્કની શીટ્સને સ્ટેક્સમાં એકસાથે બાંધવામાં આવે છે અને શિપમેન્ટની રાહ જોવા માટે વેરહાઉસમાં ખસેડવામાં આવે છે.
લાકડાની જેમ, પ્લાયવુડનો સંપૂર્ણ ટુકડો હોઈ જ શકતો નથી. પ્લાયવુડના બધા ટુકડાઓમાં ચોક્કસ સંખ્યામાં ખામીઓ હોય છે. આ ખામીઓની સંખ્યા અને સ્થાન પ્લાયવુડ ગ્રેડ નક્કી કરે છે. બાંધકામ અને ઔદ્યોગિક પ્લાયવુડ માટેના ધોરણો નેશનલ બ્યુરો ઓફ સ્ટાન્ડર્ડ્સ અને અમેરિકન પ્લાયવુડ એસોસિએશન દ્વારા તૈયાર કરાયેલ પ્રોડક્ટ સ્ટાન્ડર્ડ PS1 દ્વારા વ્યાખ્યાયિત કરવામાં આવે છે. હાર્ડવુડ અને સુશોભન પ્લાયવુડ માટેના ધોરણો અમેરિકન નેશનલ સ્ટાન્ડર્ડ્સ ઇન્સ્ટિટ્યૂટ અને હાર્ડવુડ પ્લાયવુડ મેન્યુફેક્ચરર્સ એસોસિએશન દ્વારા તૈયાર કરાયેલ ANSIIHPMA HP દ્વારા વ્યાખ્યાયિત કરવામાં આવે છે. આ ધોરણો ફક્ત પ્લાયવુડ માટે ગ્રેડિંગ સિસ્ટમ્સ સ્થાપિત કરતા નથી, પરંતુ બાંધકામ, કામગીરી અને એપ્લિકેશન માપદંડોને પણ સ્પષ્ટ કરે છે.
ભલે પ્લાયવુડ વૃક્ષોનો કાર્યક્ષમ ઉપયોગ કરે છે - મૂળભૂત રીતે તેમને અલગ કરીને અને મજબૂત, વધુ ઉપયોગી રૂપરેખાંકનમાં પાછા એકસાથે મૂકવા - ઉત્પાદન પ્રક્રિયામાં હજુ પણ નોંધપાત્ર કચરો રહે છે. મોટાભાગના કિસ્સાઓમાં, ઝાડમાં ઉપયોગી લાકડાના માત્ર 50-75% જ પ્લાયવુડમાં રૂપાંતરિત થાય છે. આ આંકડાને સુધારવા માટે, ઘણા નવા ઉત્પાદનો વિકાસ હેઠળ છે.
એક નવી પ્રોડક્ટને ઓરિએન્ટેડ સ્ટ્રેન્ડ બોર્ડ કહેવામાં આવે છે, જે લોગમાંથી વેનીયર છોલીને કોરને કાઢી નાખવાને બદલે આખા લોગને સેરમાં કાપીને બનાવવામાં આવે છે. સેરને એડહેસિવ સાથે ભેળવવામાં આવે છે અને સ્તરોમાં સંકુચિત કરવામાં આવે છે જેથી દાણા એક દિશામાં ચાલે. આ સંકુચિત સ્તરો પછી એકબીજા સાથે કાટખૂણે દિશામાન થાય છે, જેમ કે પ્લાયવુડ, અને એકબીજા સાથે જોડાયેલા હોય છે. ઓરિએન્ટેડ સ્ટ્રેન્ડ બોર્ડ પ્લાયવુડ જેટલું મજબૂત હોય છે અને તેની કિંમત થોડી ઓછી હોય છે.
પોસ્ટ સમય: ઓગસ્ટ-૧૦-૨૦૨૧